Custom Solutions
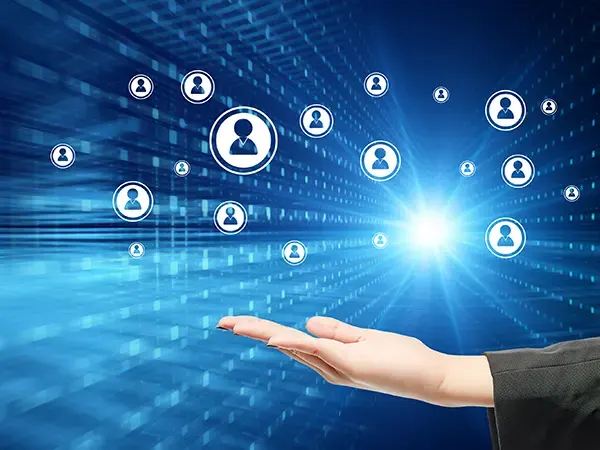
Customization: We are a factory that can provide customized parameters. We can offer standardized models or customize according to customer requirements
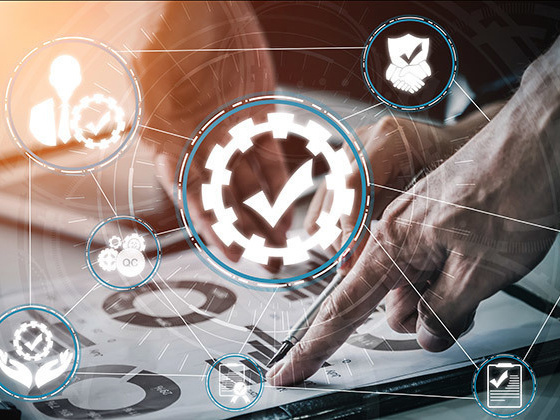
Complete certification: We hold multiple product certificates and patents, have passed the ISO9001 quality management system certification, and possess UL,TUV,KC,PSE,CE,CQC, and CCC certificates. All our products comply with the environmental protection testing requirements of ROHS and Reach
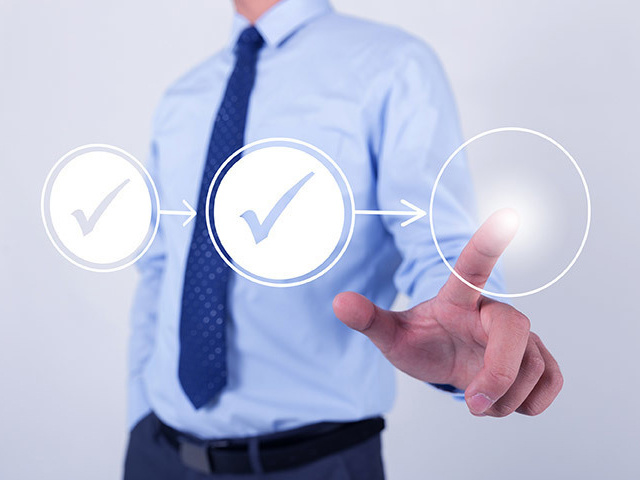
Technical Strength: We have a professional engineering team that can provide technical support. Standardized production workshops and a complete quality inspection process can ensure the quality of our products
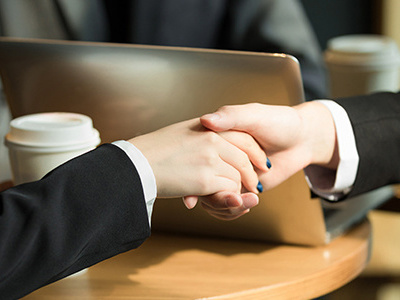
Cargo Transportation: We have rich experience in import and export and can deliver goods to all over the world. We can also provide door-to-door express delivery services.
FAQ
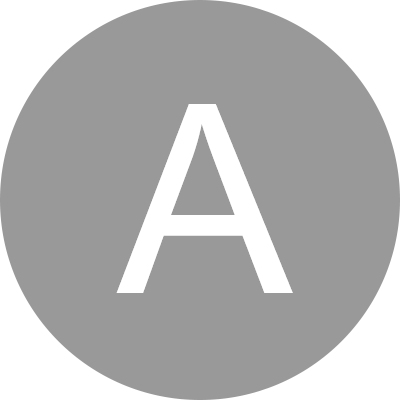
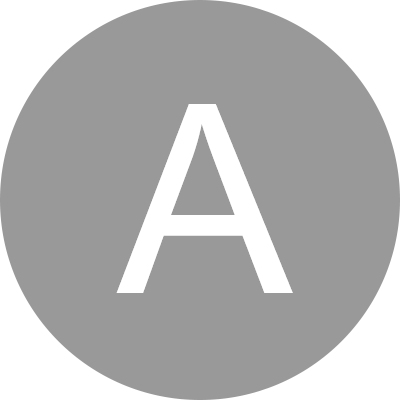
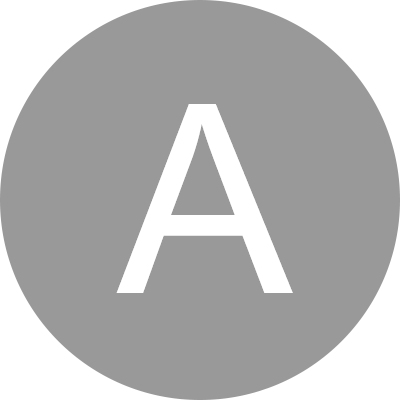
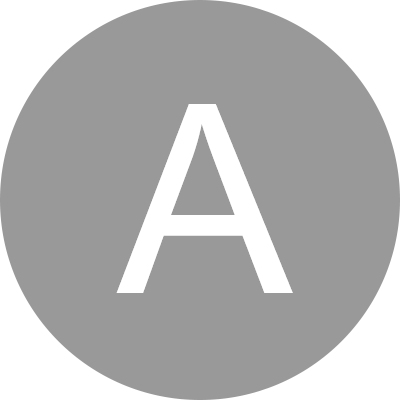
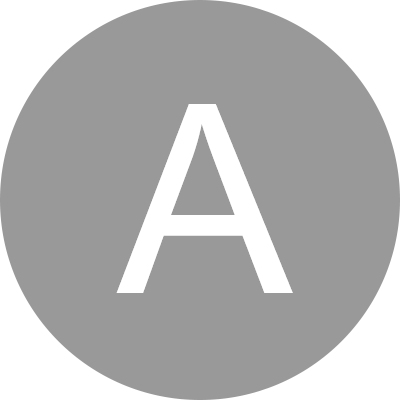